Los sectores de la siderurgia y el cementero, son clave para la construcción de edificios de grandes y pequeñas proporciones, vehículos, presas y puentes, pero estas industrias están entre las más sucias del planeta.
La producción de cemento genera 2.300 millones de toneladas de dióxido de carbono al año, y la fabricación de hierro y acero libera unos 2.600 millones de toneladas, es decir, el 6,5% y el 7,0% de las emisiones mundiales de CO2, respectivamente (según IEA).
Esto se debe en parte a las grandes cantidades en las que se utilizan estos materiales: el hormigón es el segundo producto más consumido del planeta, después del agua potable, que por sus métodos de producción emiten CO2 para alcanzar las temperaturas extremas necesarias en los procesos de fabricación.
Se necesitan urgentemente formas más limpias de fabricar y utilizar el cemento y el acero. Por ello, la revista científica, Nature, destacó nueve prioridades de investigación y acción:
Utilizar las últimas tecnologías
La mejora del aislamiento de las plantas industriales puede ahorrar 26% de la energía utilizada; el perfeccionamiento de las calderas reduce las necesidades energéticas hasta 10%; y el uso de intercambiadores de calor puede disminuir la demanda de energía del proceso de refinado en 25%.
Las plantas antiguas e ineficientes suelen ser superadas por instalaciones más modernas, por lo que las industrias se vuelven más eficientes con el tiempo. En la actualidad, las plantas de cemento más eficientes solo pueden ahorrar 0,04% de energía al año mediante la actualización de las tecnologías. Queda mucho por hacer.
Usar menos
En la actualidad, el mundo produce 530 kilogramos (k) de cemento y 240 k de acero por persona y año. Según la Agencia Internacional de la Energía (IEA), unos cambios pequeños pero significativos en los códigos de construcción y en la formación de arquitectos, ingenieros y contratistas podrían reducir la demanda de cemento hasta 26%, y la de acero 24%.
Materiales alternativos con una menor huella de carbono para un uso determinado, como el aluminio, podrían sustituir al acero en algunos productos, incluidos los vehículos.
Reinventar la producción de acero
Así se produce: el coque (derivado del carbón) alimenta los altos hornos en los que los minerales de hierro se reducen químicamente a hierro metálico a temperaturas de hasta 2.300 °C; el coque se quema para producir monóxido de carbono, que reduce el mineral a hierro y CO2.
Luego, el hierro fundido se refina en acero, normalmente en un horno de carbón, pero a veces (sobre todo cuando se recicla chatarra) en un horno de arco eléctrico (EAF, por sus siglas en inglés), cuyo proceso emite 1.800 kilogramos de CO2 o más por tonelada de acero.
Sin embargo, se pueden utilizar otras sustancias para reducir los minerales: alrededor del 5% del acero mundial ya se fabrica mediante procesos de «hierro reducido directamente» (DRI) que no requieren coque, y suelen utilizar hidrógeno y CO (derivados del metano o del carbón).
Al utilizar gas derivado del metano y electricidad renovable para alimentar un horno eléctrico, estas plantas siderúrgicas emiten 700 kilogramos de CO2 por tonelada de acero, 61% menos que las basadas en el coque.
El uso exclusivo de hidrógeno para el DRI reduciría las emisiones a 50 k o menos por tonelada de acero, una reducción del 97%. Algunas empresas de Europa, China y Australia están realizando pruebas, y se prevé que varias plantas abran sus puertas en 2025 o 2026. El reto es que este proceso requiere mucho hidrógeno.
Producir todo el acero de esta manera significaría más del doble de la producción mundial de hidrógeno, de 60 a 135 millones de toneladas anuales, pero la mayor parte del hidrógeno barato procede del gas natural, que libera CO2. Una opción más ecológica, la electrolización, es 2,5 veces más cara.
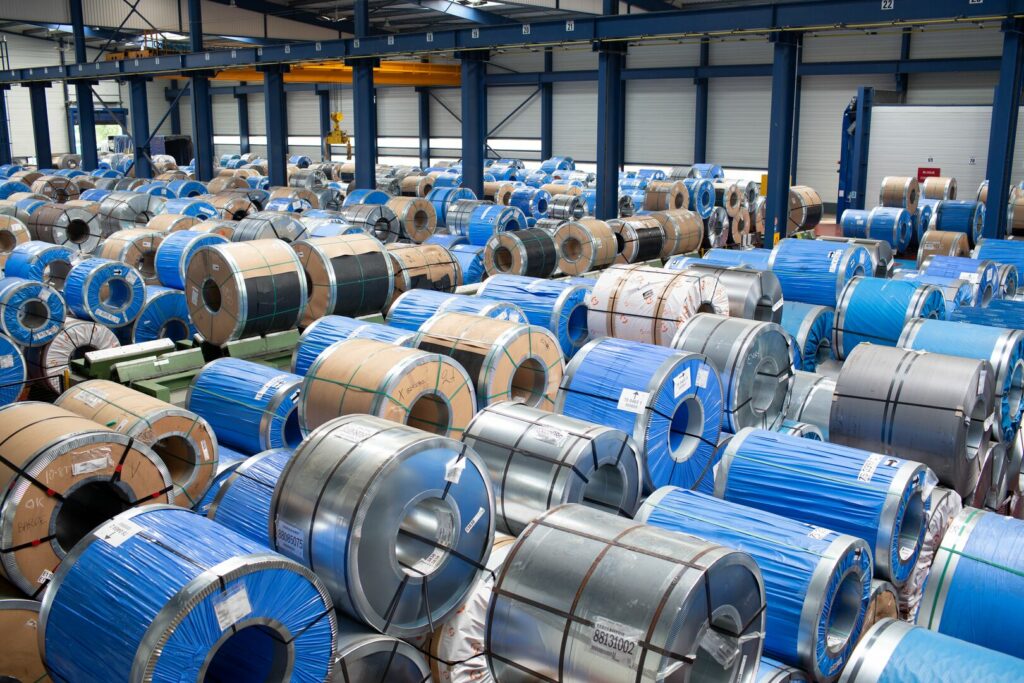
Reinventar el cemento
La producción de cemento Portland, el tipo más común, comienza con la calcinación de la piedra caliza, que se calienta a temperaturas superiores a 850 °C para formar cal y CO2. La cal se combina con arena y arcilla en un horno a 1.450 °C para crear el clinker (producto intermedio).
Alrededor del 60% de las emisiones de una planta de alta calidad proceden de la reacción de calcinación, y la mayor parte del resto del combustible quemado. En total, el proceso produce 800 k de CO2 por tonelada de cemento en una planta media, y 600 k en una planta de primera calidad.
El cemento puede fabricarse sin piedra caliza: El cemento de oxicloruro de magnesio (llamado sorel), por ejemplo, existe desde 1867, pero no se ha comercializado porque tiene baja tolerancia al agua. Se están investigando decenas de variantes, pero habrá que modificar los códigos, diseños y prácticas, lo que llevará más de una década.
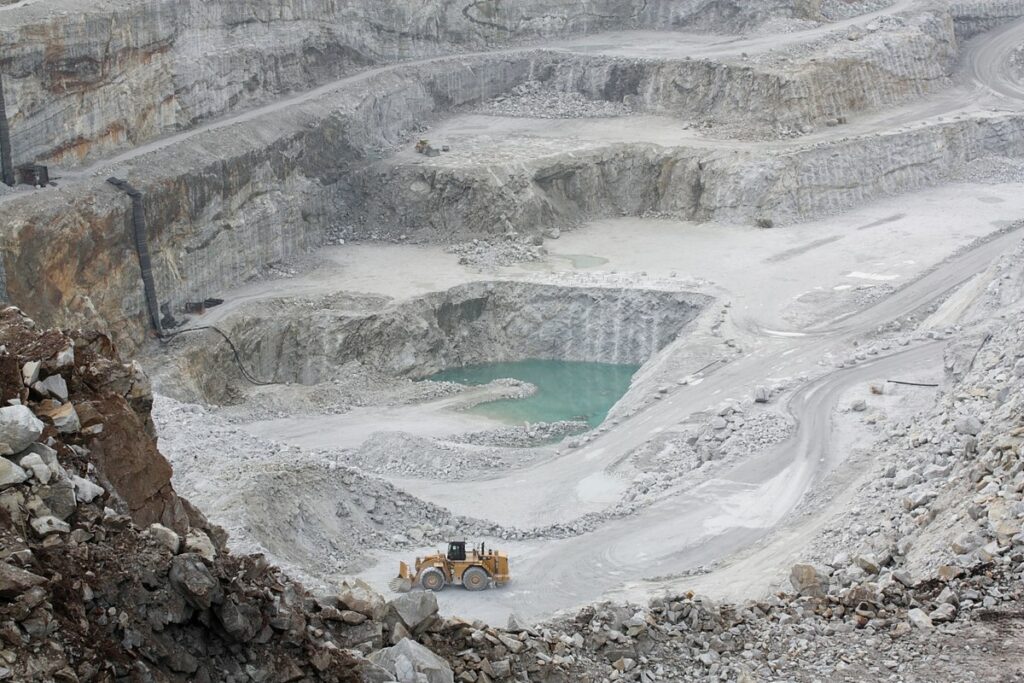
Intercambio de combustibles
En el caso del acero, resulta tentador proponer la sustitución del carbón y el coque por carbón vegetal u otras formas de biomasa, pero el cultivo de biomasa para obtener energía puede entrar en conflicto con las necesidades de tierra para la agricultura, y no todas las cosechas de biomasa son sostenibles.
El carbón vegetal es demasiado débil (comparado con el coque) para soportar las capas de material en los altos hornos, por lo que debe replantearse el procesamiento del acero, que es una solución mejor.
En relación al cemento, los residuos sólidos municipales o basura clasificada, pueden utilizarse como combustible alternativo: las altas temperaturas del horno incineran los materiales tóxicos de los residuos, y las cenizas pueden incorporarse al clinker.
Hasta el 57% de la energía de la empresa mexicana Cemex en las plantas del Reino Unido procede de estos combustibles alternativos, y el consumo de combustibles alternativos de la empresa británica Hanson se sitúa en 52%, una estrategia que debería fomentarse.
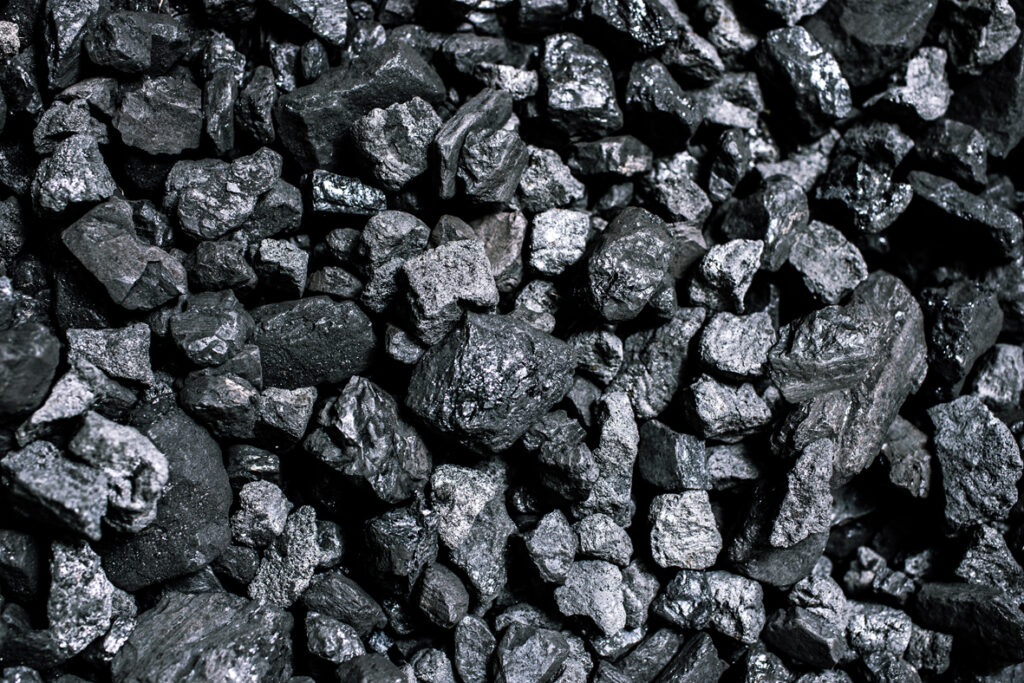
Captura de carbono
La captura de carbono, o CCS, por sus siglas en inglés, consiste en captar el CO2 y encerrarlo bajo tierra, que será esencial para reducir las emisiones de la producción de cemento, y también para el acero.
La CCS está relativamente avanzada en otras industrias, pero está infrautilizada, ya que en la actualidad solo se captura y almacena el 0,1% de todas las emisiones mundiales. Unas pocas plantas de acero y hormigón están probándola.
Almacenar CO2 en el hormigón
El cemento se convierte en hormigón añadiendo agua, arena y piedras, y la adición de CO2 puede fortalecerlo. Si el CO2 representa el 1,3% del peso del hormigón, la dureza puede aumentar en torno al 10%, y reducir la cantidad de cemento necesaria en una estructura, junto con las emisiones netas, en 5%.
Tanto el cemento como el hormigón absorben el CO2 del aire al convertir los componentes a base de calcio en piedra caliza. En teoría, se podría reabsorber aproximadamente la mitad de las emisiones del proceso de fabricación del cemento, pero los materiales tendrían que ser triturados al final de su vida útil para que las partículas de hormigón fueran más pequeñas y el CO2 pudiera difundirse mejor.
Reciclar el acero
El acero puede reciclarse eficazmente mediante un horno de arco eléctrico. Una cuarta parte de la producción de acero actual se basa en chatarra reciclada. A nivel mundial, se espera que la producción reciclada se duplique para el año 2050, reduciendo las emisiones entre 20% y 25% respecto a la actualidad.
Sin embargo, actualmente no es posible reciclar el acero de forma infinita, debido a los compuestos indeseables (especialmente el cobre) que se acumulan, aunque podría frenarse clasificando mejor la chatarra y rediseñando los productos para que el cableado de cobre sea más fácil de eliminar.
Subvencionar los cambios
Hay que superar los obstáculos económicos para que las industrias pesadas con bajas emisiones de carbono alcancen escalas de producción al año.
Se espera que la descarbonización total con CCS duplique el costo del cemento Portland, que actualmente es de 100 dólares por tonelada, y las subvenciones tendrían que ser equivalentes. Además:
- Se prevé que el acero con cero emisiones cueste entre 20% y 40% más que el acero estándar, que suele costar 600 dólares por tonelada, y las subvenciones tendrían que alcanzar los 240 dólares por tonelada.
- En el caso de la Unión Europea, podría costar hasta 200.000 millones de dólares en 10 años. Los productores tendrán que soportar la mayor parte de esos costos, y los usuarios y fabricantes se verán menos afectados.
- El acero descarbonizado solo añadiría entre 0,5% y 2% al precio de un vehículo, y hasta 15% del costo de construcción de un edificio (que en sí supone entre 1% y 3% del valor total de la propiedad).
Deberían establecerse políticas para fomentar estos desarrollos. Ha llegado el momento de que la producción de acero y cemento ayude, en lugar de obstaculizar, la carrera hacia el cero neto.
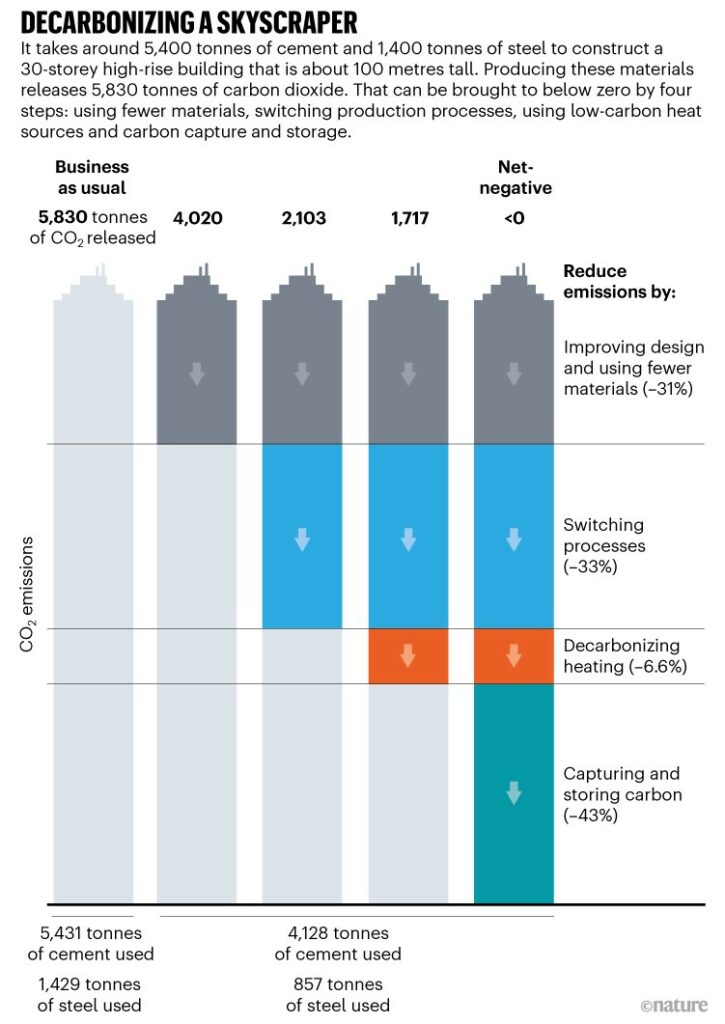
Con información de Nature
Redacción | Antonio Vilela