Cement and steel are essential ingredients in buildings, vehicles, dams, bridges and large-scale construction, but these industries are among the dirtiest on the planet.
Cement production generates 2.3 billion tons of carbon dioxide per year, and iron and steel manufacturing releases some 2.6 billion tons, or 6.5% and 7.0% of global CO2 emissions, respectively (according to IEA).
This is partly due to the large quantities in which these materials are used: concrete is the second most consumed product on the planet, after drinking water, whose production methods emit CO2 to reach the extreme temperatures required in the manufacturing processes.
Cleaner ways of manufacturing and using concrete and steel are urgently needed. For this reason, the scientific journal, Nature, highlighted nine priorities for research and action:
Using the latest technologies
Improving insulation in industrial plants can save 26% of the energy used; upgrading boilers reduces energy needs by up to 10%; and using heat exchangers can reduce the energy demand of the refining process by 25%.
Older, inefficient plants are often overtaken by more modern facilities, so industries become more efficient over time. Currently, the most efficient cement plants can only save 0.04% energy per year by upgrading technologies. Much remains to be done.
Using less
The world currently produces 530 kilograms (k) of cement and 240 k of steel per person per year. According to the International Energy Agency (IEA), small but significant changes in building codes and in the training of architects, engineers and contractors could reduce cement demand by up to 26% and steel demand by 24%.
Alternative materials with a lower carbon footprint for a given use, such as aluminum, could replace steel in some products, including vehicles.
Reinventing steel production
Here’s how it’s produced: coke (derived from coal) fuels blast furnaces where iron ores are chemically reduced to metallic iron at temperatures of up to 2,300 °C; the coke is burned to produce carbon monoxide, which reduces the ore to iron and CO2.
The molten iron is then refined into steel, usually in a coal-fired furnace, but sometimes (especially when scrap is recycled) in an electric arc furnace (EAF), the process of which emits 1,800 kilograms of CO2 or more per ton of steel.
However, other substances can be used to reduce ores: about 5% of the world’s steel is already made by “direct reduced iron” (DRI) processes that do not require coke, and typically use hydrogen and CO (derived from methane or coal).
By using methane-derived gas and renewable electricity to power an electric furnace, these steel plants emit 700 kilograms of CO2 per ton of steel, 61% less than coke-based plants.
Using only hydrogen for DRI would reduce emissions to 50 k or less per ton of steel, a 97% reduction. Some companies in Europe, China and Australia are conducting trials, with several plants expected to open in 2025 or 2026. The challenge is that this process requires a lot of hydrogen.
Producing all the steel this way would mean more than doubling the world’s hydrogen production from 60 to 135 million tons annually, but most of the cheap hydrogen comes from natural gas, which releases CO2. A greener option, electrolysis, is 2.5 times more expensive.
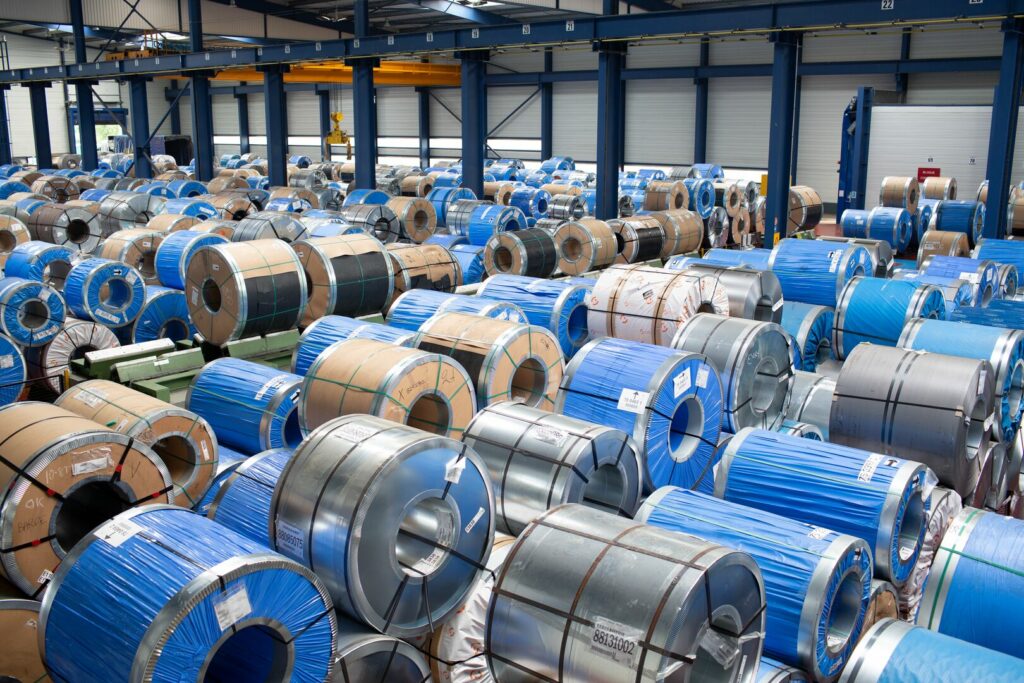
Reinventing cement
The production of Portland cement, the most common type, begins with the calcination of limestone, which is heated to temperatures above 850 °C to form lime and CO2. The lime is combined with sand and clay in a kiln at 1,450 °C to create clinker (intermediate product).
About 60% of the emissions from a high-grade plant come from the calcination reaction, with most of the remainder from the fuel burned. In total, the process produces 800 k CO2 per ton of cement in an average plant, and 600 k in a premium plant.
Cement can be made without limestone: Magnesium oxychloride cement (called sorel), for example, has been around since 1867, but has not been commercialized because it has low water tolerance. Dozens of variants are being researched, but codes, designs and practices will have to be modified, which will take more than a decade.
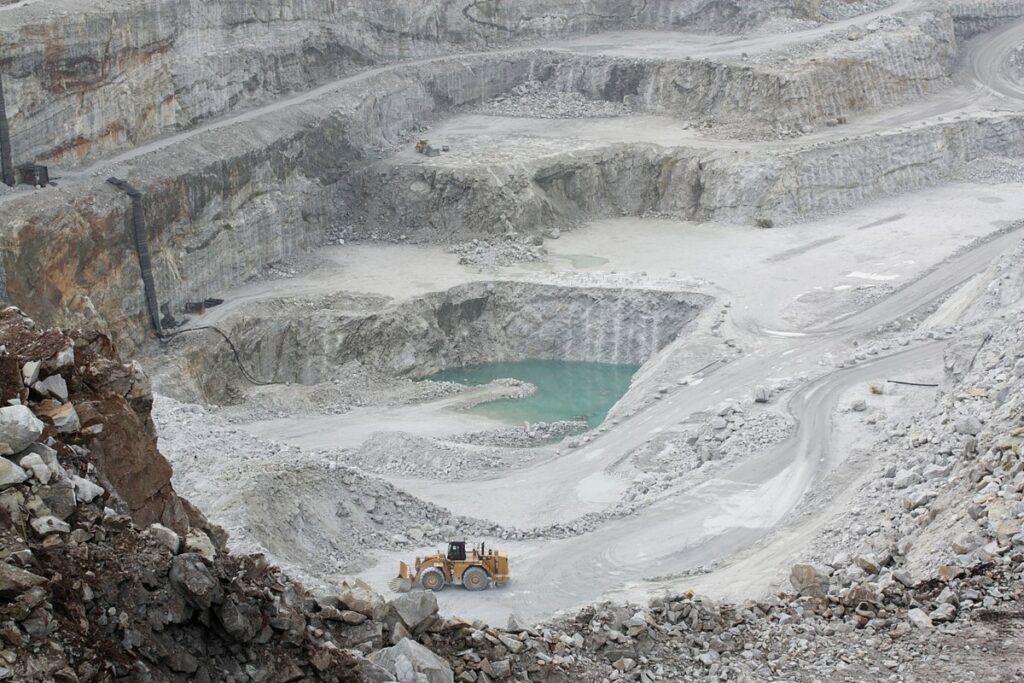
Fuel switching
For steel, it is tempting to propose replacing coal and coke with charcoal or other forms of biomass, but growing biomass for energy can conflict with land requirements for agriculture, and not all biomass crops are sustainable.
Charcoal is too weak (compared to coke) to support the layers of material in blast furnaces, so steel processing must be rethought, which is a better solution.
In relation to cement, municipal solid waste, or sorted garbage, can be used as an alternative fuel: the high kiln temperatures incinerate the toxic materials in the waste, and the ash can be incorporated into the clinker.
Up to 57% of Mexican company Cemex’s energy in UK plants comes from these alternative fuels, and UK company Hanson’s alternative fuel consumption stands at 52%, a strategy that should be encouraged.
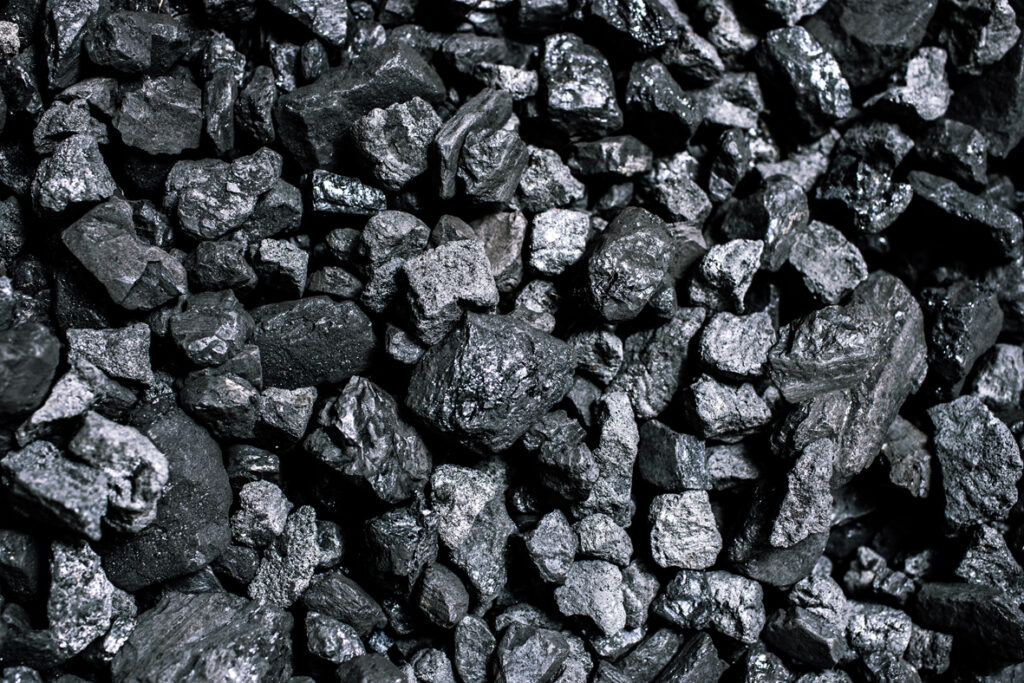
Carbon capture
Carbon capture, or CCS, involves capturing CO2 and locking it underground, which will be essential for reducing emissions from cement production, and also for steel.
CCS is relatively advanced in other industries, but is underutilized, as only 0.1% of all global emissions are currently captured and stored. A few steel and concrete plants are testing it.
Storing CO2 in concrete
Cement is made into concrete by adding water, sand and stones, and the addition of CO2 can strengthen it. If CO2 accounts for 1.3% of the weight of concrete, hardness can increase by about 10%, and reduce the amount of cement needed in a structure, along with net emissions, by 5%.
Both cement and concrete absorb CO2 from the air by converting the calcium-based components into limestone. In theory, about half of the emissions from the cement manufacturing process could be reabsorbed, but the materials would have to be crushed at the end of their useful life so that the concrete particles would be smaller and the CO2 could be better diffused.
Recycling steel
Steel can be effectively recycled using an electric arc furnace. A quarter of current steel production is based on recycled scrap. Globally, recycled production is expected to double by 2050, reducing emissions by 20% to 25% compared to today.
However, it is not currently possible to recycle steel infinitely, due to the undesirable compounds (especially copper) that accumulate, although this could be curbed by better sorting scrap and redesigning products to make copper wiring easier to dispose of.
Subsidizing change
Economic hurdles must be overcome for low-carbon heavy industries to reach production scales per year.
Full decarbonization with CCS is expected to double the cost of Portland cement, which is currently $100 per ton, and subsidies would have to be equivalent. In addition:
- Zero-emission steel is expected to cost 20% to 40% more than standard steel, which typically costs $600 per ton, and subsidies would have to reach $240 per ton.
- In the case of the European Union, it could cost as much as $200 billion over 10 years. Producers would have to bear most of those costs, with users and manufacturers less affected.
- Decarbonized steel would add only 0.5% to 2% to the price of a vehicle, and up to 15% of the cost of constructing a building (which itself accounts for 1% to 3% of the total value of the property).
Policies should be put in place to encourage these developments. The time has come for steel and cement production to help, rather than hinder, the race to net zero.
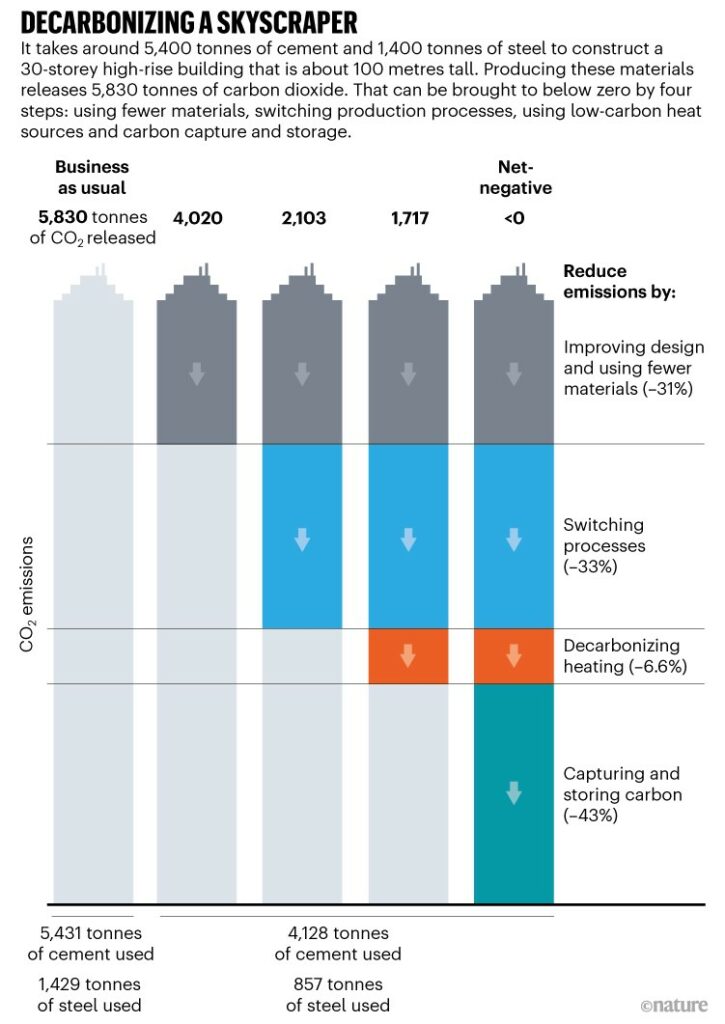
With information from Nature